成形刀具毕业设计开题报告精选
论文堡
日期:2023-11-20 17:09:09
点击:494
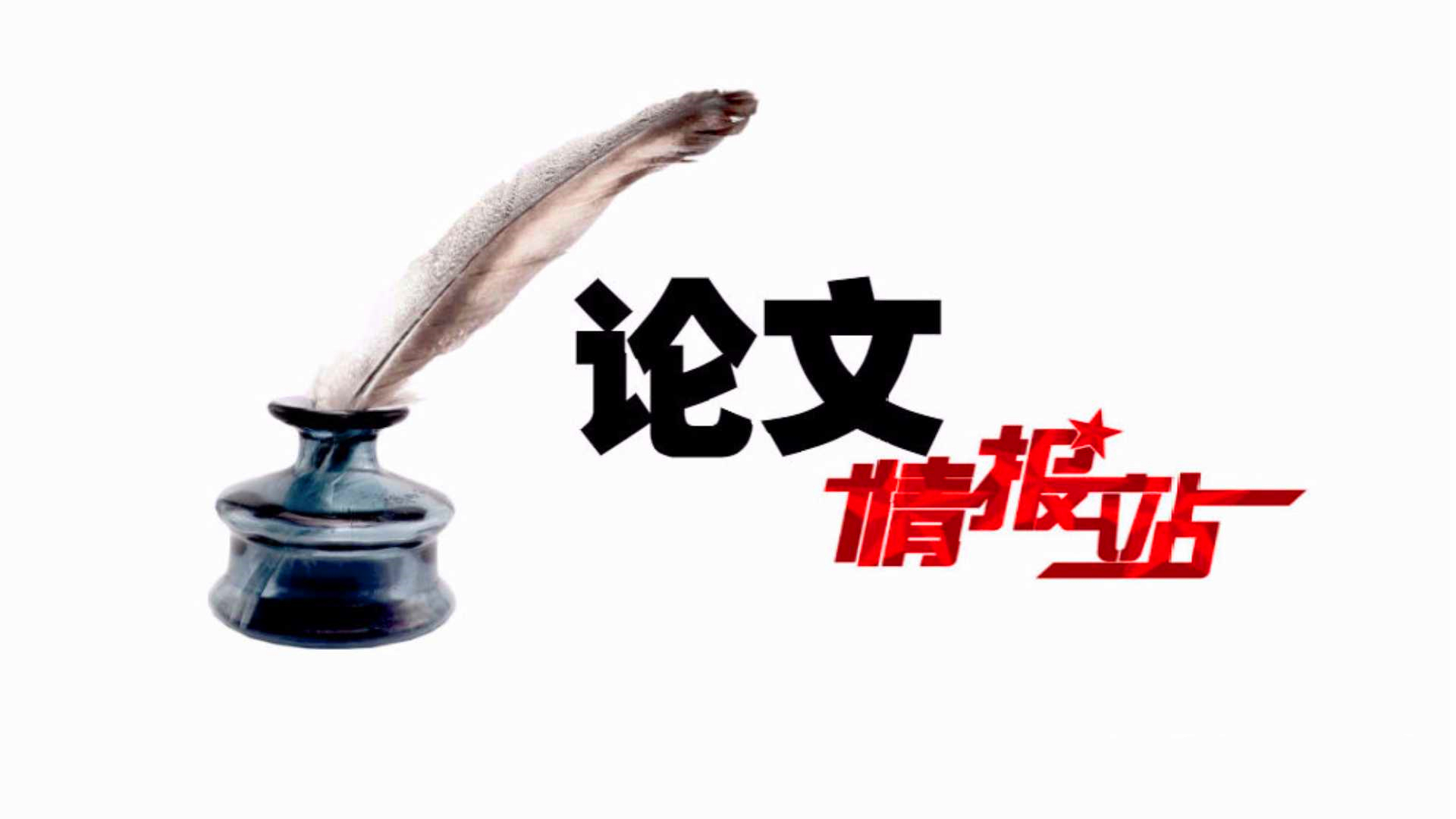
本文是一篇开题报告,参考文献是在学术研究过程中,对某一著作或论文的整体的参考或借鉴。征引过的文献在注释中已注明,不再出现于文后参考文献中。(以上内容来自百度百科)今天论文堡为大家推荐一篇开题报告,供大家参考。
一、数控渐进成形技术介绍
学者schmoeckel在他的着作中预言随着自动控制技术的不断发展进步,板料成形设备将会变得更加灵活。leszak在其申请的专利中首次提出了利用简单成形工具对板件进行加工的板料无模成形思想,但受限于当时的技术水平这种技术没有进一步向前发展。后来随着相关技术的不断发展,直到上个世纪90年代,松原才正式提出了板料数控渐进成形技术。
板料数控渐进成形技术引入“分层制造”的思想,首先将要加工的零件在高度上离散成若干层,再由cad/cam软件在每层沿零件轮廓生成相应的加工轨迹,简单的成形工具头沿着该轨迹对板件进行逐层加工,得要想要加工的零件。由于数控渐进成形是对板料进行逐层逐点进行加工,靠局部变形的积累获得整个零件,因此具有加工方式灵活、加工精度高等优点,能够成形出形状复杂的钣金零件。数控渐进成形技术从零件的三维结构设计到零件的加工轨迹生成再到零件最终成形都具有很强的灵活性,零件的尺寸或者形状变动时只需在cad/cam软件里改动零件模型即可。因此,该技术特别适合用于钣金类新产品的开发、试制及小批量生产。
板料数控渐进成形技术按其加工方式分为单点(负)渐进成形和双点(正)渐进成形。单点渐进成(single point incremental forming-spif)是一种不需要任何模具支撑的渐进成形方式。金属板被夹具固定在支架上,板下面悬空,工具头沿特定的轨迹由金属板四周向中心逐渐加工,此时金属板在力的拉伸作用下变形。零件成形过程中金属板料只跟工具头接触,成形过程中不需要模具支撑,因此单点渐进成形具有加工方式灵活、加工范围广、对设备依赖性不强、占用生产资源少等特点。此外,只需要在cad软件里改变零件几何模型就可以获得不同的成形轨迹,进而加工出相应形状的零件,所以单点渐进成形的操作性较好,但是因为成形过程中只是工具头和金属板的接触,系统刚度相对较小,成形后零件容易发生回弹,导致零件成形精度较差。
二、数控渐进成形优缺点
不同与冲压等塑性加工工艺,数控渐进成形是金属板件塑性加工的一种新的成形方式,主要有以下优点:
1.无模加工
渐进成形不需要专门的成形模具即可对金属板进行加工,特别是单点渐进成形技术,真正实现了无模具加工;即使是双点渐进成形也仅仅需要简单的模具,而且模具的制作可以是代木、纤维等材料,相对于冲压模的制作能大大节省时间成本和资金成本。
2.成形设备简单、成本低
渐进成形技术对设备的依赖性不高,普通的数控铣床进行简单的改造后就可以达到专用渐进成形机床的加工效果,对板料的渐进成形可以在普通数控铣床、渐进成形专用机床、数控加工中心等设备上实现;用来进行渐进成形刀具只是简单的圆形成形工具头,工具头不需要特殊的加工处理,只需保证硬度和表面粗糙度即可,这也降低了加工成本。
3.适合新产品的开发
市场上常见的商用cad/cam软件里就可实现从零件结构设计到加工参数优化再到成形轨迹生成整个过程的无缝衔接;当零件尺寸需要改动时,只需在软件中改动相应的结构模型就可以实现成形轨迹的改变。
4.复杂板料零件成形
由于渐进成形是对板料进行逐点逐层成形因此可实现对复杂钣金类零件的成形且成形精度高。
5.成形力小
零件渐进成形过程中只有工具头底部很小的区域与板料相接触,每层板料变形区域也仅限于该区域,且工具头在相邻加工层之间的进给量δz一般为0.2mm-1mm,因此所受成形力较小。
6.成形过程无噪音污染,对环境友好
零件渐进成形时,特别是进行单点渐进加工时,金属板和工具头的接触区域很小,加工过程中不会出现振动、冲击等现象,整个加工过程中几乎无噪声污染。
三、数控渐进成形研究现状
板料数控渐进成形技术是在现代社会消费者对产品多样化、个性化需求越来越多的背景下提出的,是一种新型的适合新产品开发、试制的制造技术,该技术的进一步发展不仅可以丰富塑性加工理论的知识体系,还具有广阔的工业应用空间。数控渐进成形技术自被提出以来,便凭借自身的优点引起国内外大量学者的广泛关注。目前,对该技术的研究主要集中在下几个方面:
成形极限图(flc)通常用来描述一种工艺的成形性能。大量研究表明渐进成形技术的成形极限图大致是一条位于第一象限负斜率的直线,而传统的成形极限图是一条v线,如图1.6所示。因此,渐进成形技术能显着提升材料的加工潜力,成形出大应变的零件。hagan和jeswiet对比研究了旋转成形、旋压成形和渐进成形三种板料成形技术的成形特征和成形机理,凸显了板料渐进成形技术的优势。jackson和allwood对拼焊铜板进行了渐进成形,研究零件成形过程中金属板的变形过程和变形机理。作者分别测量了单点渐进成形和双点渐进成形后零件厚度方向上的应变分布,发现在与工具头运动方向相切的方向上,板料主要发生拉伸和剪切变形,与在工具头运动平行的方向上,板料主要发生剪切变形;作者还发现随着拉伸和剪切作用的不断加剧,零件实际测量厚度跟正弦曲线预测厚度之间的误差会逐渐增大。s. gatea等研究了主要成形参数对板件成形性能的影响,发现零件经多道次渐进成形后壁厚分布更均匀;增量步长对板件成形性能的影响还不十分明确;增加主轴转速或者减小工具头进给速度都能使板件成形性能提高;小尺寸圆形工具头螺旋轨迹加工时,板件极限成形角较大。c.raju等将几个薄铜板叠加在一起进行单点渐进成形,分别得到每块薄铜板的成形极限图,研究每块薄铜板的成形性能。
刘兆兵等通过试验验证了板料的成形性能跟成形角度和刀具轨迹的垂直进给量有关,作者还研究了不同成形参数对工具头与金属板之间成形力的影响。马琳伟等数值模拟不同成形轨迹下零件渐进成形过程,作者将零件分成四个不同的变形区,探讨每个变形区的变形特点和变形过程。
四、提纲
致谢
摘要
abstract
第一章
1.1 引言
1.2 数控渐进成形技术
1.2.1 数控渐进成形技术介绍
1.2.2 数控渐进成形基本流程
1.2.3 数控渐进成形重要几何参数
1.3 数控渐进成形优缺点
1.3.1 数控渐进成形的优点
1.3.2 数控渐进成形的缺点
1.4 数控渐进成形研究现状
1.5 课题目的和主要内容
1.5.1 课题研究的目的
1.5.2 课题研究的主要内容
1.6 本章小结
第二章 曲面零件单点渐进成形质量及成形机理分析
2.1 引言
2.2 曲面零件单点渐进成形缺陷分析
2.2.1 表面压痕
2.2.2 平缓曲面处成形质量和垂直尺寸精度
2.2.3 成形时间
2.3 单点渐进成形机理分析
2.3.1 单点渐进成形应力状态
2.3.2 单点渐进成形应变状态分析
2.3.3 单点渐进成形零件厚度
2.4 本章小结
第三章 单点渐进成形有限元模型的建立
3.1 引言
3.2 单点渐进成形的有限元模型
3.2.1 实体模型
3.2.2 单元的选择
3.2.3 材料模型
3.2.4 网格划分
3.2.5 摩擦和接触
3.3 成形轨迹
3.3.1 工具头运动轨迹设计原则
3.3.2 轨迹生成和加载
3.4 本章小结
第四章 曲面零件单点渐进成形刀具轨迹优化(一)
4.1 引言
4.2 基于增量角度 δθ 的优化方法
4.3 试验验证
4.3.1 零件模型
4.3.2 试验设备和材料
4.3.3 试验方案
4.4 试验结果及分析
4.4.1 表面痕迹
4.4.2 零件平缓表面处成形质量和垂直尺寸精度
4.4.3 成形时间
4.5 有限元数值模拟
4.5.1 零件厚度
4.5.2 等效塑性应变
4.5.3 等效应力
4.5.4 尺寸精度
4.6 斜壁零件成形试验
4.6.1 试验方案
4.6.2 成形精度
4.6.3 零件厚度
4.6.4 成形时间
4.7 本章小结
第五章 曲面零件单点渐进成形刀具轨迹优化(二)
5.1 引言
5.2 基于增量弧长s_0的优化方案
5.3 试验验证
5.3.1 试验方案
5.4 试验结果及分析
5.4.1 表面痕迹
5.4.2 零件平缓表面处成形质量和垂直尺寸精度
5.4.3 成形时间
5.5 有限元数值模拟
5.5.1 零件厚度
5.5.2 等效塑性应变
5.5.3 等效应力
5.5.4 尺寸精度
5.6 两种优化方法的对比
5.6.1 操作性
5.6.2 试验效果
5.7 另外一种曲面零件成形实例
5.8 本章小结
第六章 总结与展望
6.1 总结
6.2 展望
参考文献
五、课题目的和主要内容
课题研究的目的数控渐进成形技术早在上世纪90年代就被有关学者提出,但至今为止仍没有大规模的应用于工业生产中,成形质量缺陷是制约该技术发展的重要因素,因此提高零件单点渐进加工质量是国内外学者研究的重点。本课题首先旨在总结归纳曲面零件单点渐进成形质量缺陷及其原因。其次,提出改善曲面零件单点渐进成形表面质量的一般性方法并通过试验验证。最后,运用有限元数值模拟,对比分析不同工艺参数对曲面零件单点渐进成形性能的影响,为实际加工时参数的选择提供参考。
本课题针对变角度曲面零件渐进成形后表面质量差的问题,主要做了以下几项工作:
1)总结归纳曲面零件单点渐进成形质量缺陷及其原因。
2)提出一种基于零件截面曲线形状用增量角度dθ来控制增量步长dz的方法,建立增量步长dz与增量角度dθ之间的计算关系,并将此方法成功应用于变角度曲面零件成形,通过试验对比该方法与传统加工方法在零件表面压痕、平缓曲面处成形质量、成形尺寸误差、成形时间等方面的区别;使用该方法加工斜壁零件,在零件厚度、零件尺寸精度、加工时间等方面与固定增量步长成形方法做对比。
3)提出一种基于零件截面曲线形状用增量弧长s0来控制增量步长dz的方法,建立增量步长dz与增量弧长s0之间的计算关系,以变角度曲面零件为例试验验证该方法的可行性,试验对比研究该方法与传统加工方法在零件表面压痕、平缓曲面处成形质量、成形尺寸误差、成形时间等方面的区别。
4)使用ansys/workbench有限元软件数值模拟曲面零件渐进成形过程,分别模拟不同增量步长δz、不同增量角度δθ和不同增量弧长s0时的曲面零件成形过程,对比分析不同成形方法成形过程中金属板塑性应变、零件成形厚度、零件成形精度等方面的差别。
六、进度安排
20xx年11月01日-11月07日 论文选题、
20xx年11月08日-11月20日 初步收集毕业论文相关材料,填写《任务书》
20xx年11月26日-11月30日 进一步熟悉毕业论文资料,撰写开题报告
20xx年12月10日-12月19日 确定并上交开题报告
20xx年01月04日-02月15日 完成毕业论文初稿,上交指导老师
20xx年02月16日-02月20日 完成论文修改工作
20xx年02月21日-03月20日 定稿、打印、装订
20xx年03月21日-04月10日 论文答辩
七、参考文献
[1]e. quigley, j. monaghan .metal forming:an analysis of spinning processes, journal ofmaterials processing technology.2000, 103(1): 114-119.
[2]kang d c, gao x c, meng x f, et al. study on the deformation mode of conventionalspinning of plates[j]. journal of materials processing technology, 1999, 91(1-3):226-230.
[3]jurisevic b, kuzman k. water jetting technology: an alternative in incremental sheet metalforming[j]. the international journal of advanced manufacturing technology, 2006,31(1):18-23.
[4]李明哲,陈建军,隋振,等。板材三维曲面多点成形技术[j].新技术新工艺,2000(10):27-29.
[5]li m, liu y, su s, et al. multi-point forming: a flexible manufacturing method for a 3-dsurface sheet[j]. journal of materials processing technology, 1999, 87(1–3):277-280.
[6]park j j, kim y h. fundamental studies on the incremental sheet metal forming technique[j].
journal of materials processing technology, 2003, 140(1–3):447-453.
[7]schmoeckel d. developments in automation, flexibilization and control of formingmachinery[j]. cirp annals - manufacturing technology, 1991, 40(2):615-622.
[8]leszak e. apparatus and process for incremental dieless forming: us, us 3342051 a[p].1967.
[9]松原茂夫。数值控制逐次成形法。塑性と加工。1994(11):1258-1263.
[10] hagan e, jeswiet j. a review of conventional and modern single-point sheet metal formingmethods[j]. proceedings of the institution of mechanical engineers part b journal ofengineering manufacture, 2003, 217(2):213-225.
相关文章
人力资源新增
人力资源热点